Aluminium is the future!
Aluminium is the future and Jönköping University is the champion of Aluminium!
Swedish Aluminium
The Swedish Aluminium industry has, for a long time, focused on scrap recycling. As a result, aluminium recycling is Sweden is well-deveöoped. Recycled material consists of both post-consumer scrap and process scrap. Process scrap is a foundation for economically viable manufacturing. The change of using post-consumer scrap in the manufacturing chain is due to its poorer quality. Reintroducing a poor quality material is by definition more challenging. These challenges are critical to keeping the Aluminium carbon footprint low.
The foundry industry uses low-grade materials returns since long. Sheet producing companies do not have the same tradition. Component manufacturing out of aluminium sheet requires a high level of formability. High formability is difficult to achieve using large quantities of recycled material. This is well established for the foundry industry, but for rolled products, this is ore challenging due to requirements on affordability.
What does it take to be sustainable and circular in manufacturing?
To increase the amount recycled, it is necessary to understand the flow of the particular alloying elements critical to new alloys with higher secondary material contents. This understanding is essential to the development and increased use of sustainable Aluminium alloys in Sweden.
Today, the cost-effectiveness of material manufacturing is synonymous with the use of high amount of secondary material. Furthermore, it may improve the material management at the aluminium producers. Better management may allow for economically viable smaller batches through cost-effective alloys through the high content of secondary material.
In the long run, making aluminium product greener will improve the image and attractiveness of the Swedish Aluminium industry.
Snags and challenges!
The limiting factor today for this is the formability of rolled materials with high levels of recycled materials. To address this effectively, both processing and alloying needs the full attention of researchers. A first step is to identify the available scrap types and sources to understand how a sustainable material supply can be built.
The future of vehicle manufacturing is heavily influenced by available materials, and regulatory efforts, especially those regulating designers focusing on vehicle weight reduction. In the search for reduced transportation carbon footprint, weight reduction is one of the most cost-effective routes to improved energy efficiency, while maintaining or improving performance expected by consumers. Needless to say, there is a significant trend towards the use of aluminium alloys due to their attractive density and weight-reducing potential, cost, and performance. An interesting side-effect of the chase for weight reduction is also that the material and manufacturing energies will increase in importance in the life-cycle analysis of vehicles.
A scrap flow outlook
International Aluminium Institute (http://www.world-aluminium.org/statistics/ ) identifies that the main flow of Aluminium is primary Aluminium, and the secondary materials are process scrap, fabricator scrap and post-consumer scrap. There are other scrap flows as well, as depicted in the figure below. It should be noted that in 2020 the primary aluminium use to 72500 kton. The process scrap corresponds to 44300kton, while the fabricator scrap is 13400kton and the post-consumer scrap 18200kton.
In 2040 this is projected to be 100800kton (+39%). The projected process scrap should be 63600kton (+44%). The fabricator scrap and the post-consumer scrap was projected to 19500 (+46%) and 30100 (+65%), respectively; Figure 1b. The appreciated development is such that the growth in the scrap market exceeds that of the primary aluminium market.
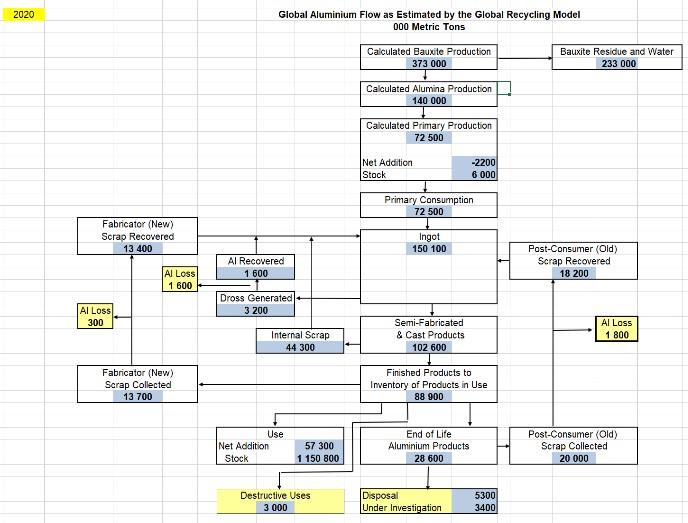
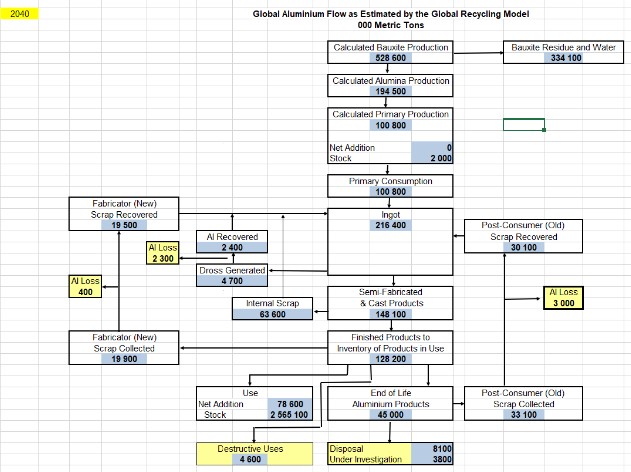
The projected, most significant, growth product segments are in the automotive and transport industries, together with the building industry. This implies that the secondary aluminium industry is projected to grow significantly and that there is a strong potential to create a competitive advantage in developing a capability to increase the amount of secondary material in high-performance products. During this period the amount of Aluminium in use was projected to become more than double from 1150800kton to 2565100kton
Elements impurities and sustainability
In previous research, and in my Vertikals blog, I discussed this, as it turns out that for the manufacturing of semifinished goods the most beneficial alloying elements with energy consumption, carbon footprint and water usage in relation to strength increase were Mn and Zn. In addition, Si and Mg commonly dominate as alloying elements for the cast components. This is another interesting coincidence.
This is, in turn, important for rolled and formed sheets. (Jarfors et al Sustainability 2020, 12, 1059; doi:10.3390/su12031059). The challenge is to use recycled material in sheet forming and other forming processes. Secondary material often displays significantly lower formability and this is a real limitation. Dispinar et al ( TMS Light Metals January 2011, DOI: 10.1007/978-3-319-48160-9_127) stared that the root cause to this problem is the detrimental effects of oxides of the performance of the material.
Kore et al ( 2017 J. Phys.: Conf. Ser. 896 012007) on the other hand showed that low-grade recycled material such as chips and turnings, and be formed and deep drawn.
The creation of a sustainable future
New processes such as Hot Forming and Cold die quenching have the potential to effectively produce high performance and complex light-weight products in a single process step and will provide a significant addition to the manufacturing processes.
Researchers such as Ismail et al (Proceedings of the 17 MS 129th Int. AMME Conference, 19-21 April, 2016) concluded that new processes do place stringent requirements on the material formability. Das et al (Materials Science Forum Vols. 519-521 (2006) pp. 1239-1244), on the other hand, concluded that the challenges in the design of a recycling friendly alloy. Among the key challenges to be met in creating this ideal recycling friendly alloy were identified as:
- Maximise recovery of used aluminium products and components for recycling;
- Automate and optimise the pre-sorting, shredding, and separation technologies;
- Identify more useful byproducts to handle residual elements, e.g., Fe.
- Broaden the number of available aluminium alloys whose specifications will readily accept recycled metal and will perform well in high-quality, value-added products.
Material design
Das et al (Materials Science Forum Vols. 519-521 (2006) pp. 1239-1244) further states that as a possible rationale for creating more recycling-friendly aluminium alloy composition limits the following should be considered
- For major alloying elements in a particular series (e.g., Cu in the 2xxx series, Si and Mg in the 6xxx series, etc.), propose relatively broad specification limits.
- For limits on impurities (elements not usually required or desired, e.g., Fe, Ni, and V), propose more tolerant (i.e., higher) limits. To the degree potentially practical, adjust the maximum limits on impurities to the levels of those elements typically found in recycled metal
Das et al (Materials Science Forum Vols. 519-521 (2006) pp. 1239-1244) concluded that a suitable target application for a new recycle-friendly aluminium alloy include many of the same as for their existing counterparts with tighter limits such as
- 3xxx – Heat-exchanger tubing, chemical piping
- 4xxx – Forged or cast engine parts
- 5xxx – Tankage plate; housing components
- 6xxx – Extruded structural components
For a commercial success of wrought sheet based material. The above matters lead to that in order to capture the market potential and the possible competitive advantages for the increased use of secondary Aluminium it is essential first to understand the materials flow in Sweden and Europe. A critical element is to understand how steady and stable flows can be achieved and also to understand how the materials in these flows can be combined with the process scraps to provide an alloy rich in secondary Aluminium without compromising properties nor formability.
Detta är en bloggtext. Det är skribenten som står för åsikterna som förs fram i texten, inte Jönköping University.