How to choose materials for a sustainable future
Today sustainability is on everyone’s lips and it is important. Greta Thunberg talks about the CO2-budget and the politicians are waking up. More importantly, consumer behaviour is changing and we change the way we eat, shop, and transport ourselves. Transports today take up roughly 28% of all the energy that we use and it is predominantly fossil-based energy. Currently, the solution to this is electrification and it is driven by the US-based Tesla and the Chinese company BYD. Volvo and Scania are also joining this race.
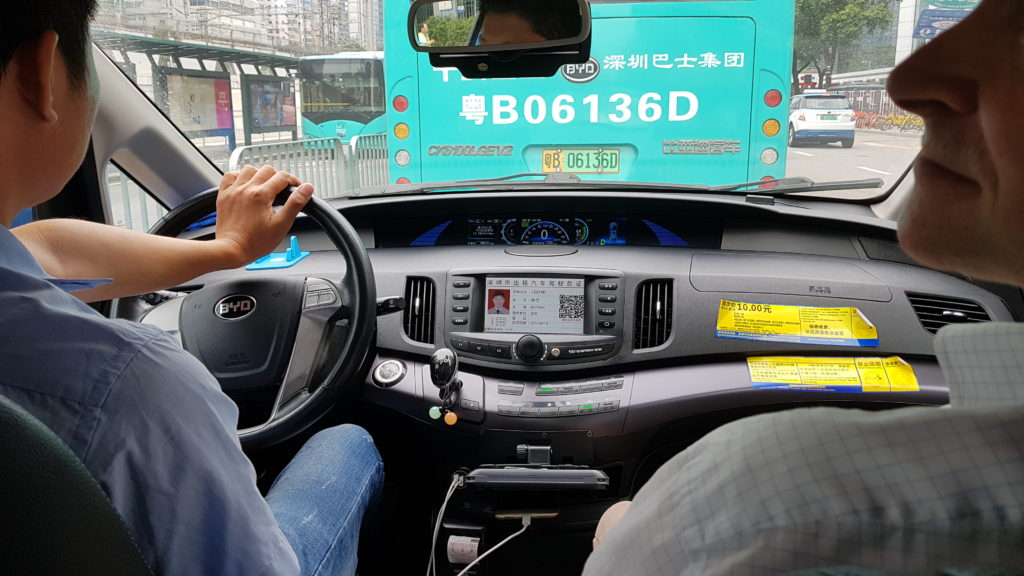
How can we create a sustainable future?
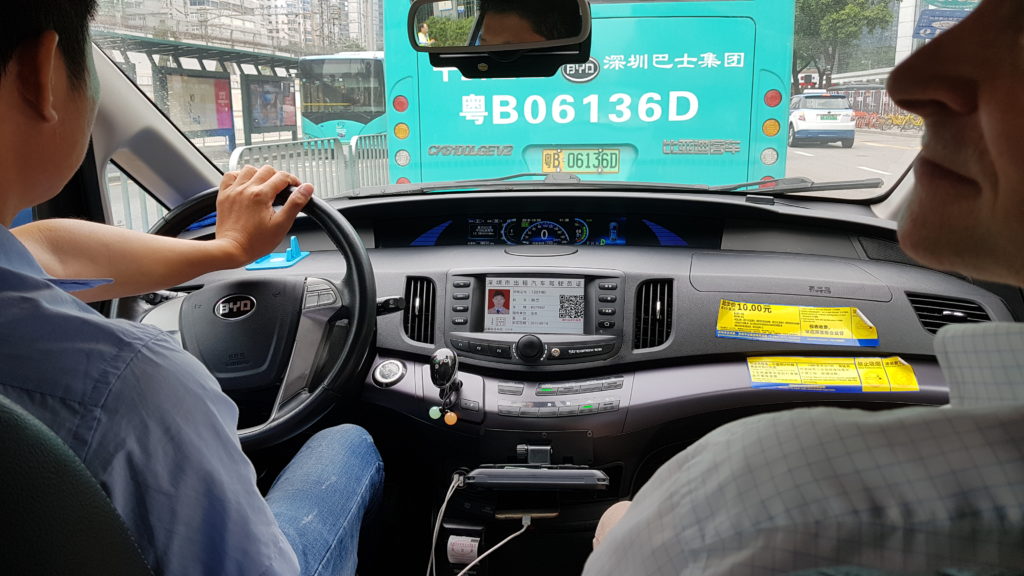
There is however a BIG problem!
The first issue is that 28% of the energy is quite a lot and our electrical supply system will struggle to reach this level. Investment level is high and the existing solutions are often fossil-based too! A result is that we reduce the particle emissions in the cities but only to move them to the fossil-based powerplants and the net effect on our carbon footprint is zero. So to sum things up the problem moves around and there is really no solution to this! Or is there?
Is there really no solution?
I am technology optimist so I think that there is a way out! In the short run there is the less popular solution involving fission-based nuclear power and in the long-run fusion power. There are also great possibilities for expanding sun-, water- and wind-power. All these, however, take time and this is something that we do not have!
In a paper by Serrenho and co-authors, the effect of vehicle weight reduction was analysed and was concluded that during the transition to a fossil-free electricity generation, weight reduction of vehicles could produce greater cumulative emissions savings by 2050 than those obtained by the electrification alone. Weight saving is a key success factor and in this aspect aluminium and magnesium alloys are the most effective engineering solutions due to their low densities. This has also been realised by automotive companies. Projections say that somewhere between 250 and 500 kg of aluminium will be used in passenger cars with maintained safety. This is, in turn, a fantastic opportunity and a significant challenge for the aluminium industry. To reach this level without causing too much carbon emissions, new strategies to improve properties are important as high-performance parts need to be made from recycled aluminium which today is difficult. The main issues are impurity management and the enrichment of iron, that caused strength problems, and copper, that is ecotoxic and both require limitations. To create new alloys that will support this is thus a priority for the aluminium industry.
How to create a good aluminium alloy then?
In a newly published paper, I address this together with some of my Chinese colleagues. This work is a collaboration between Jönköping University and the China Academy of Machinery Science and technology.
In all light-weight design, it is all about reducing the amount of material used. To keep the component stiffness where needed you need design freedom and this is best offered by casting processes. To provide material that is ductile for crash safety casting is not always the best choice and it is here new materials and processes can solve the problems.
The paper takes a look at what the best alloying elements that will allow for high strength and ductility through a measure called ultimate tensile strength that includes both the effect of strength and failure characteristics of the material. It looks at the energy footprint, carbon footprint and water usage as water is a future critical and scarce resource.
The first main conclusion we already know and that is to not use iron in the material so removing iron is a critical skill to develop. But how to alloy aluminium to make it strong and better for the environment?
Well, we got a real surprise!
Most cast materials today ate Aluminium-Silicon based materials. Our surprise was that Manganese was such a clear best candidate for all aspect and was only beaten by Si when it came to efficient water usage. Energy and carbon footprint also including the effect of cost Manganese was the best choice. The second-placed element was Zinc which also was a surprise. In cast alloys, Manganese is added to reduce the negative effects of Iron so the fact that Manganese came out on top is really good news for the Aluminium industry.
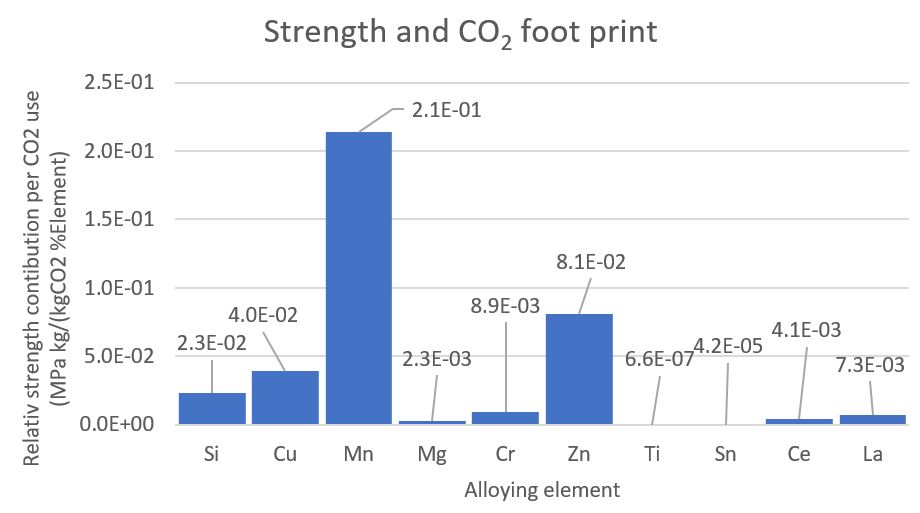
In addition to this when studying the carbon footprint, both Cerium and Lanthanum was better than Magnesium. Most alloys today are based on Aluminium Silicon and Magnesium. So in order to improve sustainability, new alloy concepts based on Aluminium, Zinc, Manganese and Lanthanum should be given priority. It should also be noted that from a cost point of view this would not really change.
To read the full paper :
Jarfors, A.E.; Du, A.; Yu, G.; Zheng, J.; Wang, K.
On the Sustainable Choice of Alloying Elements for Strength of Aluminum-Based Alloys. Sustainability 2020, 12, 1059.
Click on the following link
https://www.mdpi.com/2071-1050/12/3/1059
Detta är en bloggtext. Det är skribenten som står för åsikterna som förs fram i texten, inte Jönköping University.